Preface
Concrete mixing plants are essential equipment for concrete production, with a wide variety of types. Among them, foundation free concrete mixing plants are widely welcomed for their convenient and fast installation and operation characteristics. This article will provide a detailed introduction to the installation process of a foundation free concrete mixing plant.
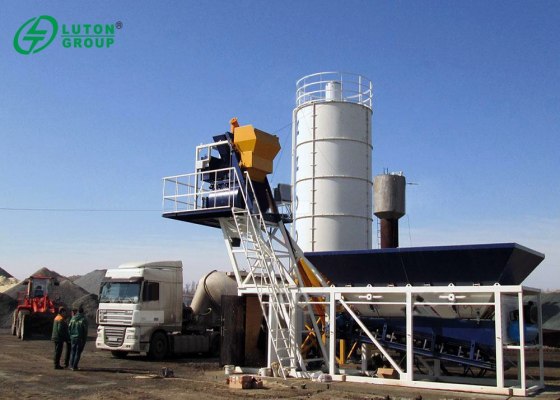
Introduction to Ground Free Base Stations
A foundation free concrete mixing plant, as the name suggests, is a type of concrete mixing plant that does not require foundation construction. It can be installed on any flat and hardened ground, greatly simplifying the installation process and reducing installation costs.
On Site Installation Process Of Foundation Free Concrete Mixing Plant
- Confirm Installation Site
Choose a flat site to ensure that the ground is sturdy and free from large stones or obstacles such as tree roots. At the same time, it is necessary to ensure that the site area is large enough to accommodate all the equipment of the mixing plant. Consider maintaining space and secure buffer zones in the future.
- Equipment Entry
Ensure that all equipment is not damaged during transportation and has been properly secured according to transportation requirements. Before entering the installation site, a preliminary inspection should be conducted, and any damage should be dealt with promptly.
- Equipment Assembly
According to the instructions in the equipment manual, assemble all equipment together to form a complete mixing plant. This step requires professional personnel to operate to avoid errors that may cause equipment damage. During assembly, attention should be paid to the interfaces of each component to ensure their tight connection and prevent leakage or loosening.
- Electrical Connection
Ensure that all electrical equipment complies with local safety standards and make correct electrical connections according to the instructions. All cables and wires should be properly fixed to avoid pulling or pulling randomly. At the same time, it is necessary to ensure that all electrical equipment is grounded to prevent accidental electric shock.
- Inspection And Debugging
After assembly is completed, conduct a comprehensive inspection and debugging of the mixing plant to ensure that all equipment is working properly. This step should include but is not limited to the inspection of key components such as electrical systems, hydraulic systems, and transmission systems. Use testing tools to perform performance tests on various systems to ensure they meet design requirements.
- Operation Training
Provide operation training to operators to ensure that they are proficient in operating the mixing plant. The training content includes but is not limited to basic operations, safety operating procedures, and emergency response methods.
- Acceptance
After all equipment is working properly and operators are proficient in operation, acceptance and delivery for use shall be carried out. This step should be carried out by professionals to ensure that all functions of the mixing plant meet the design requirements and can operate safely and stably.
- Document Organization
Organize and save all installation records, inspection records, and debugging reports for future maintenance and management purposes.
- Subsequent Maintenance
Even after the mixing plant is officially put into use, regular maintenance and inspections should be carried out to ensure its long-term stable operation.
Installation Precautions
During the installation process, it is important to ensure that the site is level and sturdy to avoid damage to the equipment. Uneven ground should be treated, such as filling or raising, to ensure the stable operation of the equipment.
The assembly of equipment should be carried out according to the instructions, and the assembly sequence or component position should not be changed arbitrarily. For complex components, seek professional assistance and do not attempt to solve difficulties on your own.
During the debugging process, special attention should be paid to safety to avoid accidents. For example, when debugging a hydraulic system, it should be ensured that all components are fixed and there is no risk of leakage.
Operators must undergo professional training and be familiar with the operation and maintenance of the equipment. They should understand the basic mechanical principles and safety operating procedures to prevent equipment damage or personal injury caused by unsuitable operation.
During use, it is necessary to regularly inspect and maintain the equipment to ensure its stability and service life. Any faults or issues discovered should be promptly addressed and not allowed to worsen. At the same time, attention should also be paid to the maintenance and lubrication of the equipment to extend its service life.
Extra care should be taken in the maintenance and inspection of electrical systems to ensure that all electrical equipment meets safety standards and operates properly. Any electrical issues discovered should be promptly addressed to prevent electrical accidents.
Attention should be paid to the adoption of safety measures when handling hazardous chemicals. Appropriate protective equipment should be worn and safety operating procedures should be followed to prevent accidents such as chemical leaks or personnel poisoning.
Before carrying out any safety related operations, the power or hydraulic power supply should be cut off to ensure the safety of the operation.
When dealing with mechanical faults, the manufacturer’s recommendations and guidelines should be followed for repair and maintenance work. Do not attempt to self repair complex problems or modify the structure of mechanical components.
Any changes that may affect equipment performance or safety should be consulted with the manufacturer (ltconcreteplant.com) or professionals in advance, and ensure that all changes comply with relevant regulations and safety standards.
Summary
The installation process of the foundation free concrete mixing plant is simple, but it also requires professional personnel to operate and guide. Following the correct installation process can ensure the stability and efficiency of the equipment, as well as extend its service life. For users, understanding the installation process and precautions of the equipment can help them better use and maintain the equipment, and improve production efficiency. During the installation process, attention should be paid to details and the adoption of safety measures to ensure the smooth installation and long-term stable operation of the equipment. As a convenient and efficient concrete production equipment, the foundation free concrete mixing plant provides strong support for construction projects. By proper installation and use, its advantages can be fully utilized to improve production efficiency and engineering quality.